The technology needs of the Defense Department (DoD) are as varied as the department itself. In addition, each military service plans for logistics materials independent of the others, with no global visibility into resource location, status or potential demands against it. So how can cloud-based platforms help DoD attain new military readiness standards?
GovLoop recently hosted an online training titled “How DoD Can Improve Readiness” to address those issues. Speakers included:
- Kevin Sampels, Senior Business Development Executive, CACI International
- Col. Robert Henderson, Commander, 635th Supply Chain Operations Wing, United States Air Force
- Col. Kerry L. George, Deputy Director for Maintenance Policy Plans and Programs, Office of the Deputy Chief of Staff, HQDA G4
- Bill Reuter, retired Capt. of the U.S. Navy and President of R-Squared Solutions, LLC
- Mark Failor, Technical Director of SCM, CACI International
Sampels highlighted the complexity of the current and future military operating environment, which requires simultaneous operations conducted from small, dispersed bases rather than from a central location. “Whether it’s access denial, cyberattacks or kinetic attrition of forces, we can be confident that what has brought us success in the past will not necessarily make us successful in the future,” he said.
Many of the logistics processes involved today require supported and supporting agencies. While logisticians are challenged to rapidly identify, prioritize and allocate materials against the highest risks or the greatest needs. However, “a truly global enterprise platform that considers both operational and mobile logistics requirements doesn’t exist today,” Sampels said.
He added, “As our world becomes interconnected, changes have immediate impact. Disruption is the new norm.” The focus for the future lies in anticipation of action as opposed to reacting to action, and circumstances dictate that investments are focused on a configurable cloud architecture to maintain and track assets to support critical missions.
Col. Henderson next spoke about a common Air Force problem related to weapons systems, specifically the use of outdated aircrafts that were designed and built when maintenance systems were not computerized. “There was not a thought process for how we were going to manage this for the long term and now we find ourselves in 2019 with that problem,” Henderson said.
“There is no unifying cloud system that gives us visibility of our parts within the base, and that gives us visibility across the Air Force,” he continued. “There’s absolutely no visibility across the other services.”
DoD has contract obligations of about $80 billion over the next four years, but about 70 percent of that is sustainment funding and planning toward modernization. Over the last year, DoD has attempted to build an investment strategy to address this problem. One procurement is the Joint Enterprise Defense Infrastructure (JEDI), worth $10 billion, which aims to leverage a cloud computing solution to gain greater visibility across the department.
Col. George then spoke about two main efforts in maintenance: condition-based maintenance and additive manufacturing. The Army still services most of its vehicles based on time as opposed to usage. An audit found that a high percentage, somewhere in the 70 to 80 percent range, of combat systems aren’t reporting accurate mileage.
“We want to apply sensors to the vehicles in our combat systems to be able to self-report mileage using on-board diagnostics,” George said. The next step is taking that information into a cloud-based, artificial intelligence-enabled enterprise system that’s able to give a fleet diagnostic. The goal is to ultimately predict when maintenance events are going to occur.
The Army also has to be able to justify the investment in CBM+ capability. Industry can show a return on investment (ROI) for investors, but for the Army the most important driving factor is readiness.
In terms of additive manufacturing, the Army maintains a lot of legacy systems. Some of the systems are bridging systems and additive manufacturing can be used to mitigate obsolescence. George pointed out the need to manufacture as close to the point of need as possible. They want to hit that ‘economical sweet spot’ of having the equipment on time but not spending more to make the equipment than it would if they were to mass-produce it.
Reuter then spoke about how the Navy is concerned about vendor lock, which can be disadvantageous when it comes to incorporating enterprise solutions available in the market that are much more agile, effective and proven than some of their in-house efforts.
The Navy has recently developed the training and readiness accelerator and has received offers for solutions on building out an IT infrastructure that will integrate the supply system, as well as ship and aviation material readiness.
Another goal is establishing a workforce and culture that is agile and literate enough to be able to not only manage requirements for solutions but also to use them and understand their value.
“Raising the literacy of the workforce to understand how to evaluate the veracity of a particular approach or another is crucial to their vision,” Reuter said. “Digital transformation is cultural and technical. It affects everyone.”
Failor, the final speaker, tackled how technical advances improve readiness through the visual of a data tower:
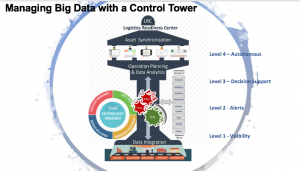
The challenge is that the data is dirty, and there isn’t a process of data cleansing. “We want to make the information available for the operational planners to do data analytics,” Failor said. “We have programs of records for supply chain and financial management across the DoD that’s facing audits now, but I think there’s a great opportunity for enterprise data management. We need to get away from the spreadsheets and look to exploit the cloud to aggregate asset data, perform data analytics and determine how your logistics posture is going to change.”
Certain technologies can support the tower, including mobile devices that can lead to easy data access, automation of overall knowledge, and 3D printing.
All of these technologies can be used to provide a more holistic modernization strategy to meet an increasingly complex military operating environment.
Photo Credit: Kevin Sampels
I attended the training live, and it was informative, even for non-military personnel. I found it interesting that the problem isn’t just that the military isn’t performing fleet maintenance enough, but sometimes it’s a case of over maintenance. So the sweet spot is leveraging technology to predict exactly when maintenance is needed.